What are the factors affecting the accuracy of centerless grinder
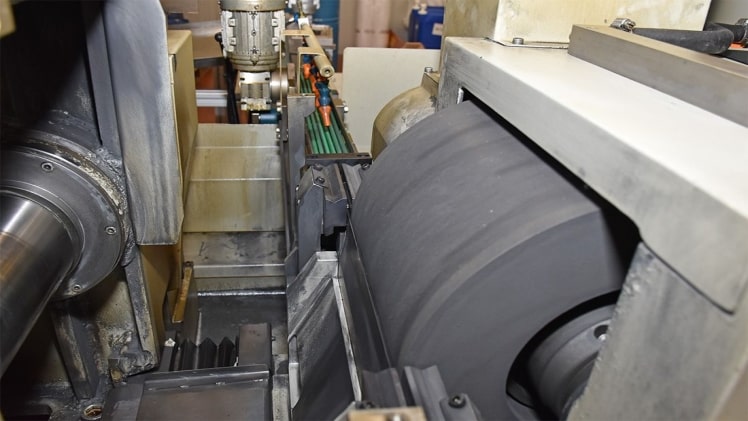
Geometric accuracy and operation accuracy of the machine tool itself; Rigidity of parts, rationality of clamping and positioning of parts, correctness of selection of machining process benchmark, rationality of heat treatment process of parts, scientificity of formulation of machining process (separation of rough and finish machining, suitability of selected machining equipment, etc.), accuracy and reliability of selected cutting tools, influence of temperature change on machine tools and parts The technical level of the operator and so on.
What are the factors affecting the machining accuracy of grinding machine
1、Oil cooler
The purpose of grinder oil cooler is to stabilize the temperature of anti-wear hydraulic oil required by the movement of drive shaft. The oil temperature is not high at the beginning, but with the passage of time, the oil temperature of anti-wear hydraulic oil will gradually rise. Then the bed of the machine tool is affected, and there will be thermal deformation. You should know that when the temperature rises by one degree, the deformation of machine tool casting bed will be 0.01mm, so it is very critical to control the oil temperature of anti-wear hydraulic oil. How to control the oil temperature, the more common way is to install an oil cooler.
2、Magnetic separator (paper tape magnetic separator)
As we all know, the grinding fluid contains slag, and the slag will be different according to different grinding workpieces. When these slag materials float in the grinding fluid and are used as a medium in grinding and processing of the grinder. These slag quality will seriously affect the finish of grinding. I believe everyone can understand this and agree with the same statement. When your workpiece is magnetically conductive, use a magnetic separator. When you have more precise machining requirements or when the workpiece is not magnetically conductive. It is recommended that you use paper tape magnetic separator (the device has paper tape adsorption function and better filtration)
3、Air conditioner
The temperature rise control of machine tool is very important, so good machine tools will be equipped with air conditioner (random air conditioner). The grinder has a heat source, namely the spindle. It can cool the spindle, which is not only conducive to the cooling of the machine tool, but also prolong the service life of the spindle. Generally, an air conditioner (random air conditioner) can be installed at the rear of the spindle, and an exhaust device is adopted at the upper part to maintain the circulation of cold air. This proposal is mainly aimed at large grinding machines, because such grinding machines have large spindle power and are easy to generate heat. The phenomenon after heating is thermal elongation, which is a fatal problem for the grinding and processing of cutting groove, and the accuracy can not be guaranteed at all.
What are the main factors affecting the surface roughness of grinding
The main factors affecting the surface roughness of grinding are:
1. Dressing of grinding wheel
The dressing of grinding wheel is to make a thread on the working surface of grinding wheel with diamond nib The smaller the trimming lead and correction depth The more the number of grinding particles, the better the contour of the repaired blade Therefore, the smaller the workpiece surface roughness value.
2. Grain size of grinding wheel
The finer the grain size of the grinding wheel. The number of grinding rods per unit area on the working surface of the CNC grinding service is more Therefore, the knife marks on the workpiece are denser and thinner Therefore, the smaller the roughness value is.
3. Hardness of grinding wheel
The hardness of the grinding wheel is too high It is not easy to fall off after passivation of grinding position The workpiece surface is strongly rubbed and squeezed It intensifies the plastic void, increases the spread value of the surface sail, and even produces surface burns. If the grinding wheel is too soft, the grinding position is easy to fall off Uneven wear will occur Binxiang’s surface roughness is better than this The hardness of the grinding wheel shall be moderate.
4. Grinding speed
Increase grinding speed It increases the number of grinding grains per unit area of the workpiece and increases the number of scratches At the same time, the plastic deformation decreases, so the surface roughness decreases. The plastic deformation decreases at high speed because the propagation speed of plastic deformation at high speed is less than that of grinding The material is too late to deform.
5. Grinding radial feed and number of smooth grinding
Grinding with radial feed and incremental grinding increases the cutting depth and intensifies the plastic deformation Therefore, the surface roughness increases Properly increasing the number of bare feet can effectively reduce the surface roughness.
6. Circumferential feed rate and axial feed rate of lower part
The increase of the circumferential feed speed of the workpiece and the feed of the shaft LLJ will reduce the grinding w bit on the unit area of the workpiece and reduce the amount of scoring The surface roughness increases.
7. Cutting fluid
When grinding, the cutting temperature is high and the role of heat is dominant Therefore, the role of cutting fluid is very important. Cutting fluid can reduce cutting temperature and burn Washing off the fallen Lin particles and wear debris can raise the workpiece without scratching, so as to reduce the surface roughness. Workpiece materials and grinding conditions also have an important impact on surface roughness. The main factors are as follows:
1). Dressing of grinding wheel. Dressing of grinding wheel is to make a thread on the working surface of grinding wheel with diamond nib The smaller the trimming lead and correction depth The more the number of grinding particles, the better the contour of the repaired blade Therefore, the smaller the workpiece surface roughness value. Whether the diamond NIB used for dressing is stable or not has a great influence on the correction quality of the grinding wheel Figure 11 1 shows the micro edge grinded by the grinding wheel after fine correction.
2). Grain size of grinding wheel the finer the grain size of grinding wheel. The number of grinding rods per unit area on the working surface of the grinding wheel is more Therefore, the knife marks on the workpiece are denser and thinner Therefore, the smaller the roughness value is. However, if the grinding wheel with rough drawing is finely trimmed After grinding and pulling l the micro blade You can also add: R. the surface with small mountain roughness value.
3). The hardness of the grinding wheel is too high It is not easy to fall off after passivation of grinding position The workpiece surface is strongly rubbed and squeezed It intensifies the plastic void, increases the spread value of the surface sail, and even produces surface burns. If the grinding wheel is too soft, the grinding position is easy to fall off Uneven wear will occur Binxiang’s surface roughness is better than this The hardness of the grinding wheel shall be moderate.
4). Grinding speed increases the grinding speed It increases the number of grinding grains per unit area of the workpiece and increases the number of scratches At the same time, the plastic deformation decreases, so the surface roughness decreases. The plastic deformation decreases at high speed because the propagation speed of plastic deformation at high speed is less than that of grinding The material is too late to deform.
5). The radial feed of grinding is most closely related to the number of smooth grinding. The radial feed of grinding increases the cutting depth during grinding and intensifies the plastic deformation Therefore, the surface roughness increases Properly increasing the number of bare feet can effectively reduce the surface roughness.
6). The circumferential feed rate and axial feed rate of the next workpiece increase the circumferential feed rate and axial LLJ feed rate of the workpiece, which will reduce the grinding W-bit on the unit area of the workpiece and reduce the amount of scoring The surface roughness increases
7). When grinding with cutting fluid, the cutting 9 degree is high, and the role of heat is dominant Therefore, the role of cutting fluid is very important. Using cutting fluid can reduce 0 cutting degree and burn Washing off the fallen particles and wear debris I can raise the workpiece without scratching, so as to reduce the surface roughness. We must reasonably choose the cooling method and cutting fluid.
What are the factors affecting the machining accuracy of grinding machine
1、Oil cooler
The purpose of grinder oil cooler is to stabilize the temperature of anti-wear hydraulic oil required by the movement of drive shaft. The oil temperature is not high at the beginning, but with the passage of time, the oil temperature of anti-wear hydraulic oil will gradually rise. Then the bed of the machine tool is affected, and there will be thermal deformation. You should know that when the temperature rises by one degree, the deformation of machine tool casting bed will be 0.01mm, so it is very critical to control the oil temperature of anti-wear hydraulic oil. How to control the oil temperature, the more common way is to install an oil cooler.
2、Magnetic separator (paper tape magnetic separator)
As we all know, the grinding fluid contains slag quality, which will be different according to different grinding workpieces. When these slag materials float in the grinding fluid and are used as a medium in grinding and processing of the grinder. These slag quality will seriously affect the finish of grinding. I believe everyone can understand this and agree with the same statement. When your workpiece is magnetically conductive, use a magnetic separator. When you have more precise machining requirements or when the workpiece is not magnetically conductive. It is recommended that you use paper tape magnetic separator (the device has paper tape adsorption function and better filtration).
3、Air conditioner
The temperature rise control of machine tool is very important, so good machine tools will be equipped with air conditioner (random air conditioner). The grinder has a heat source, namely the spindle. It can cool the spindle, which is not only conducive to the cooling of the machine tool, but also prolong the service life of the spindle. Generally, an air conditioner (random air conditioner) can be installed at the rear of the spindle, and an exhaust device is adopted at the upper part to maintain the circulation of cold air. This proposal is mainly aimed at large grinding machines, because such grinding machines have large spindle power and are easy to generate heat. The phenomenon after heating is thermal elongation, which is a fatal problem for the grinding and processing of grooving, and the accuracy can not be guaranteed at all. The machining accuracy of cylindrical grinder depends on three aspects:
1). The correction accuracy of grinding wheel (it should be corrected in time);
2). Grinding quantity control (feed quantity control): judge the rigidity of the part according to the material, heat treatment state and workpiece size of the processed part, so as not to cause micro winding of the workpiece due to too large grinding quantity;
3). Whether the clamping of workpiece is slightly loose, etc. The above factors are based on the premise that the clearance of the spindle bearing of the grinder is normal. If there is a problem with the clearance of the spindle bearing, it will seriously affect the machining accuracy of the workpiece.